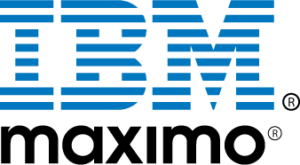

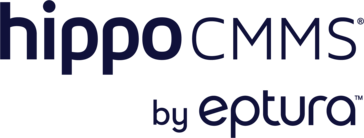


Meet us at
How you benefit from your maintenance comments
You can impact directly your OEE and machine productivity with the insights you gain from your shiftlog-, maintenance-, MES-, downtime-comments.
Reduce repeating problems
Find systematic problems in your comments and get hints how to solve them.
Share knowledge
Turn your documentation into trouble shooting knowledge.
Improve Quality
Find systematic issues in your QA/non-conformance reports by SKU
Identify preventive maintenance actions
Reduce unplanned maintenance calls by identifying avoidable production stops.
Peoplegeist helps you find classic preventive maintenance actions such as: cleaning, lubrication, replacement interval, wear & tear, …
- Fewer maintenance calls
- less stress on the team
- better reaction time
- more time for improvement work.
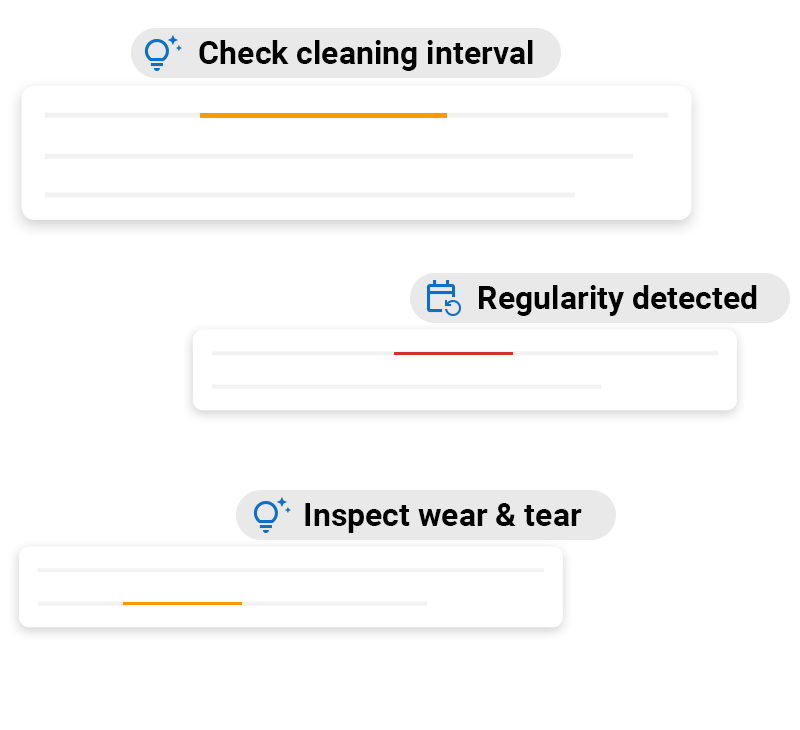
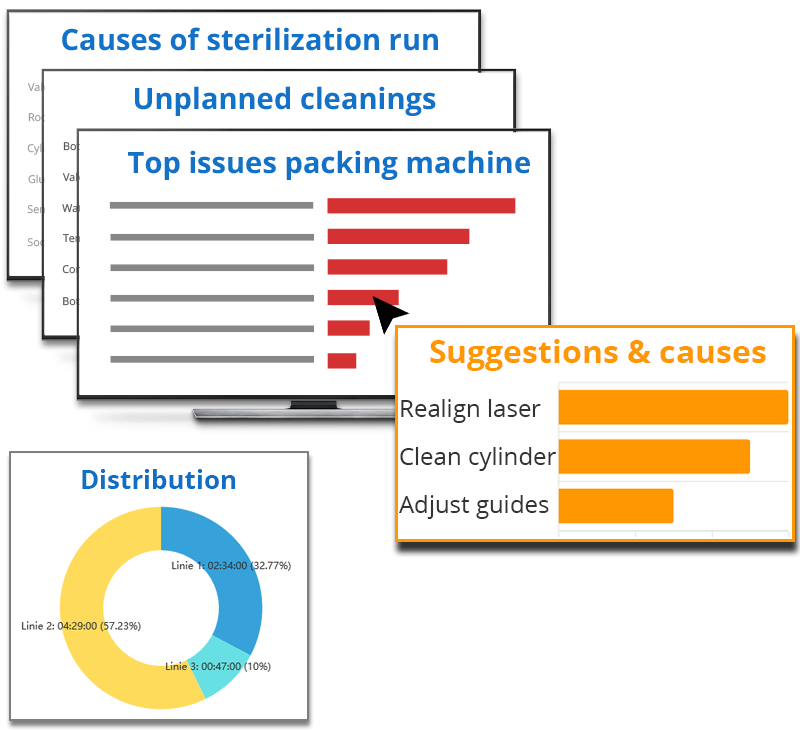
Causes behind repeating failures
Identify repeating errors with automatically generated pareto charts.
Our TextAI understands your problems in your text-comments without manual categorization or manually defined classification-tree.
Deep dive on each topic and receive hints for your root-cause analysis:
- Understand what causes lead to the problem.
- Pin down sources of an issue
Share trouble history
See Who, When, What was done in the past for specific problems.
Get the full maintenance history even if your colleagues are not on the same shift.
Find the notes of your team immediately.
Asset knowledge is shared this way automatically without any extra work needed.
The traditional approach
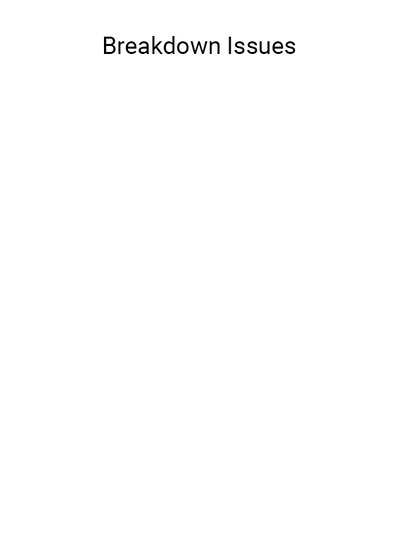
With peoplegeist
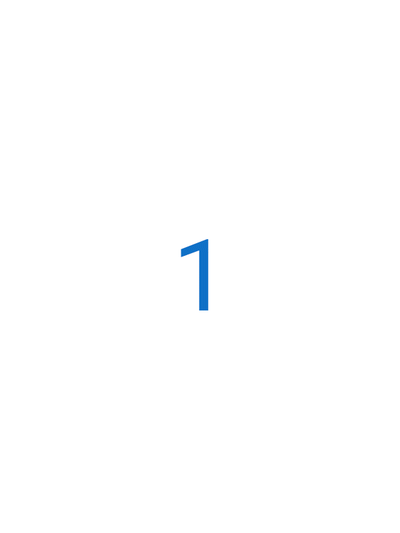
Use TextAI and NLP to analyze your maintenance comments
Peoplegeist has developed a NLP AI (natural language processing) that understands manufacturing problems and solutions in maintenance logs
To make sense of text-logs you don't need to manually categorize them anymore nor do you have to read through them one by one. Our AI will scan them for you and create breakdown analysis charts with the push of a button.
These pareto charts can be used for downtime-analysis, predict maintenance needs and find training gaps.
Once our AI has learned about your problems at the factory you can query the AI when you encounter an issue. The software can show potential solutions based on past experience.
Our software works multilingual across 50 languages. Employees can use it in their native language. Cross-lingual analysis is especially helpful to find repeating problem patterns across sites in different countries. It also helps to share knowledge across teams working in different languages.
🇫🇷 🇪🇸 🇬🇧 🇵🇹 🇵🇱 🇷🇸 🇮🇹 🇩🇪 Our AI understands the languages of your staff (50 languages)
Your shift log-, maintenance-, and MES-log - comments is a valuable treasure. They document all the problems in production and how they were resolved.
Text AI enables you to unlock this knowledge. The software automates reading through the logs and summarizes problems, resolutions and improvements found in the text.
The App automatically creates pareto charts of production issues, shows hints for the root-cause analysis, and can suggest resolution steps to speed up trouble shooting.
Benefit from the knowledge in your maintenance comments
What you can gain from your shift log-, maintenance-, and MES-log - comments.
Save downtime
Reduce downtime through shorter (MTTR) and fewer incidents (MTBF)
No IT-Project
Live in < 2 weeks. Excel export is all you need to get started
0 discussions
0 (zero) discussions about events not being categorized correctly.