HOWTO: Steigerung der Leistung deiner Linie - Quick Wins und Low Hanging Fruits
Praktische Tipps, wie du deine Produktionslinie betrachten und die Leistung steigern kannst.
Einführung
In jedem Produktionsprozess ist eine unserer Hauptanliegen, wie wir unsere Produktionseffizienz steigern können. In anderen Artikeln haben wir das Pareto-Diagramm als ein visuelles Werkzeug verwendet, um Hauptprobleme zu identifizieren. In diesem Artikel werden wir in einer praktischen Weise versuchen, wie wir die Produktion in einer Fertigungsproduktionslinie verbessern können.
In diesem Gedankengang werden wir einige Fragen ansprechen, um unsere Analyse zu initiieren.
Bedeutet die Steigerung der Produktion dasselbe wie die Reduzierung von Ausfallzeiten?
Die Steigerung der Produktion und die Reduzierung von Ausfallzeiten sind zwei äußerst wichtige Variablen, die unterschiedlich behandelt werden müssen, aber nicht dasselbe sind. Die Produktion kann auf andere Weise gesteigert werden. Zum Beispiel, indem du die Zykluszeit verbesserst oder die Anzahl der ausgeschleuderten Teile reduzierst, während die Ausfallzeiten gleich bleiben.
Wenn ich die ursprünglichen Eigenschaften des Systems beibehalte und die Ausfallzeiten reduziere, werde ich am Ende des Analysezeitraums eine höhere Produktion erreichen. Daher wird die Reduzierung von Ausfallzeiten immer ein sehr wichtiges Ziel für das gesamte Anlagenmanagement sein.
Ist die Steigerung der Produktion gleichbedeutend mit einer Verbesserung der OEE (Overall Equipment Effectiveness)?
Denke daran, dass die OEE eine Berechnung ist, die drei Variablen berücksichtigt: Verfügbarkeit, Leistung und Produktqualität. Wenn ich einen der Parameter erhöhen kann, ohne die anderen zu verringern, kann ich die Gesamteffizienz der Anlagenausrüstung (OEE) verbessern.
Im Allgemeinen kann die Produktion erhöht werden, indem die Ausfallzeiten verbessert werden (Erhöhung der Verfügbarkeit), die Leistung der Anlage verbessert wird und/oder die Anzahl der im Qualitätskontrollprozess abgelehnten Produkte reduziert wird. Im Allgemeinen kann die Steigerung der Produktion unsere OEE verbessern, solange sie keinen negativen Einfluss auf eine ihrer Variablen hat.
Aktueller Zustand visualisieren
Eine der wertvollsten Erkenntnisse zur Maximierung der Produktion besteht darin, ein umfassendes Verständnis des aktuellen Zustands deiner Produktionslinie zu gewinnen. Bei der Bewertung der aktuellen Situation ist es wichtig, Schlüsselaspekte wie die Verfügbarkeit der Anlagen und die Effizienz der Produktionslinie zu berücksichtigen.
Liste alle Maschinen und Produktionsstufen in einer Tabelle auf und notiere bei jedem Schritt:
- Gesamtverfügbarkeit der Maschine (in Stunden)
- Tatsächliche Betriebszeit der Maschine
- Geschwindigkeit (wie viele Teile pro Betriebsstunde verarbeitet werden können)
- Tageskapazität (tatsächliche Betriebszeit * Stücke/Stunde)
- Fehler/Ablehnungen pro Stunde
- Nettodurchsatz (Durchsatz - Fehler/Stunde = Gute Teile pro Stunde)
Wir haben ein vereinfachtes Beispiel für die Produktion mit 4 Schritten. Es könnte in der Lebensmittelproduktion sein.
- Schokoladenproduktion
- Herstellung von Schokoladenriegeln
- Einzelstückverpackung
- Kartonieren und Palletieren
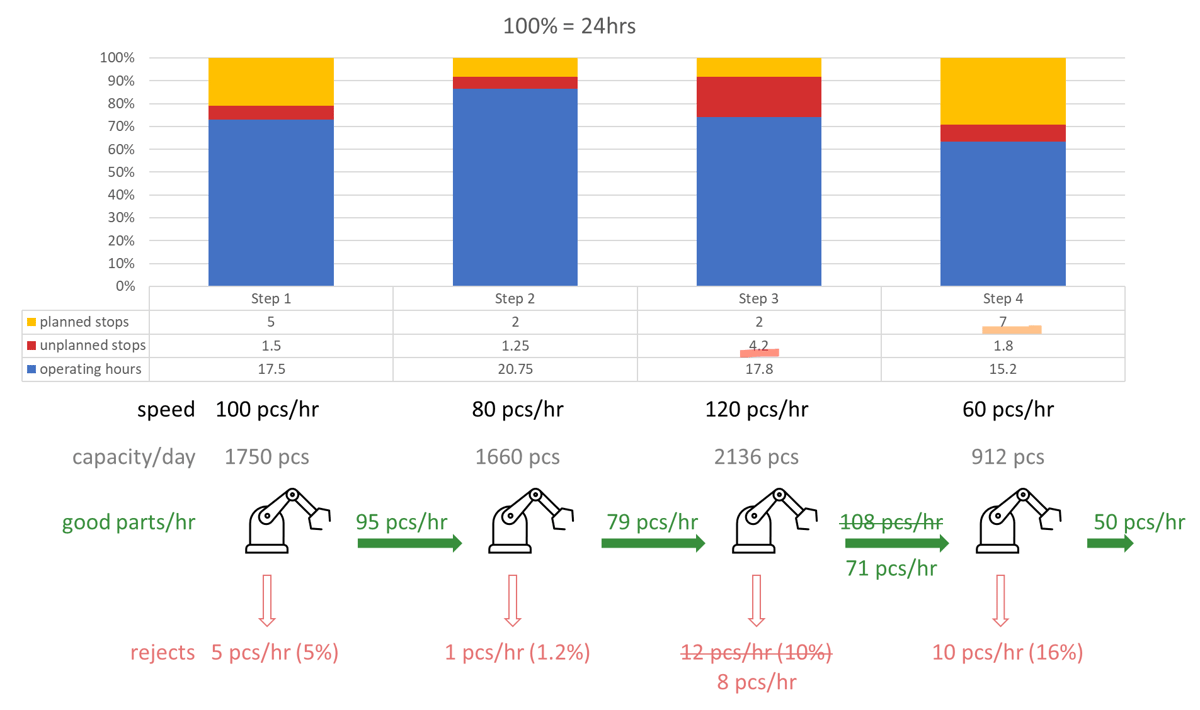
Abbildung 1: Visualisieren deiner Linie Beispiel
Was sehen wir hier: Wir beginnen mit 100 Stück/Std. und irgendwie bekommen wir am Ende nur 50 Stück/Std.
Nachdem du deinen Produktionsfluss visualisiert hast, ist es einfacher zu verstehen, was passiert, und es ist leicht zu erkennen, wie die Maschinen voneinander abhängig sind.
Instinktiv würde man Ablehnungs- und Ausfallgründe sammeln und Pareto-Diagramme erstellen. Diese Praxis kann jedoch dazu führen, dass wichtige Aspekte wie der Arbeitsablauf oder die Produktion, sowie Sicherheits- und Umweltaspekte übersehen werden.
Finde deine Engpässe
Wenn es darum geht, die Produktion zu steigern, besteht die Lösung nicht immer darin, die längsten Ausfallzeiten zu identifizieren und zu beheben. Wie im vorherigen Beispiel gezeigt, liegt der Schlüssel zur Steigerung der Effizienz manchmal darin, Engpässe in deiner Produktionslinie zu identifizieren und anzugehen. Der Engpass ist der Arbeitsbereich mit der geringsten Leistung (wenig gute Teile/Stunde). Dieser Ansatz ermöglicht es uns, von Engpass zu Engpass zu wechseln und die Effizienz der gesamten Produktionslinie iterativ zu verbessern.
Der erste Schritt in dieser Strategie besteht darin, die Station oder den Arbeitsbereich in deiner Produktionslinie zu identifizieren, der den geringsten Durchsatz aufweist. Du kannst ihn dir als das schwächste Glied in der Kette vorstellen. Wenn du dieses Glied stärkst, verbesserst du die Gesamteffizienz der Linie. Das bedeutet, dass du nicht immer längere Ausfallzeiten behandeln solltest, da sie möglicherweise nicht der limitierende Faktor in deinem Prozess sind.
In unserem Beispiel können wir sehen, dass Schritt 4 nur 60 Stück/Std. verarbeiten kann, während Schritt 3 71 Stück/Std. liefert.
Dies sehen wir auch in der Tageskapazität. Schritt 4 kann nur 912 Stück verarbeiten, während der vorherige Schritt 2136 Stück liefern konnte.
Du kannst Schritt 4 auf drei Arten verbessern:
- Niedrigere geplante Stopps: Erhöht die Betriebszeiten und somit die Gesamtkapazität
- Erhöhung der Geschwindigkeit: Steigert die Stücke/Stunde und erhöht die Kapazität
- Niedrigere ungeplante Stopps: Erhöht die Betriebszeiten und somit die Gesamtkapazität
Nicht direkt mit dem Engpass verbunden, sondern mit der Gesamtleistung, kannst du auch versuchen, die Ablehnungsrate zu reduzieren. Dadurch erhalten am Ende des Tages mehr gute Teile.
Verbesserung vom Ende der Linie aus
In unserem Beispiel sehen wir, dass die Durchflussraten zwischen allen Produktionsschritten nicht übereinstimmen. Ein Ansatz besteht darin, die Verbesserung deiner Produktionslinie am Ende zu beginnen. Wenn wir am Ende der Produktionslinie einen Engpass identifizieren, beispielsweise unsere Verpackungskapazität, spielt es keine Rolle, wie sehr wir unseren Prozess am Anfang der Linie optimieren, da unsere Gesamtproduktion durch den letzten Engpass begrenzt wird. Auf diese Weise können wir durch die Steigerung der Verpackungskapazität der Linie unsere Produktion erhöhen und potenzielle Engpässe identifizieren, um letztendlich die maximale Gesamteffizienz des Produktionssystems zu erreichen.
Erhöhung der Verfügbarkeit
Lange geplante Ausfallzeiten
In unserem Beispiel möchten wir mit der Verbesserung von Schritt 4 beginnen.
Die Ausfallzeit beträgt 1,8 Stunden/Tag und wir könnten beispielsweise mit TextAI ein Pareto-Diagramm unserer Ausfallzeitdokumentation erstellen.
Die größere Gelegenheit besteht jedoch darin, auch die geplanten Ausfallzeiten zu betrachten. Der größte Verlust bei Schritt 4 beträgt 7 Stunden geplante Ausfallzeit pro Tag.
Du kannst deine Wartungsdokumentation überprüfen und sehen, warum so viel Zeit für diese Maschine aufgewendet wird.
Liegt es an Problemen mit der Einrichtung, die länger als erwartet dauern? Gibt es Schwierigkeiten bei der Neuverkonfigurierung einer Produktionslinie? Die strategische Lösung sollte die Hauptursachen angehen, das Personal schulen und Wartungsverfahren durchführen, die Aufgaben effizienter und innerhalb der geplanten Stillstandszeiten erledigen.
Linienumstellungen
Linienumstellungen können einen kritischen Punkt in der Produktion darstellen. Es ist normal, dass diese Umstellungen nach der Durchführung einige Probleme verursachen. Um diese Situation effektiv anzugehen, wird empfohlen, die bei Linienumstellungen verwendeten Checklisten zu verbessern. Um dies zu erreichen, ist es wichtig, Maschinenbediener in den Prozess der Verbesserung der Prüflisten einzubeziehen. Durchführung von Interviews mit Bedienern und Abgleichen der erhaltenen Informationen mit Daten und Kommentaren, die von Wartungsmitarbeitern während Wartungsaufgaben an der Ausrüstung bereitgestellt werden, kann eine wertvolle Wissensquelle generieren. Diese Informationen können in Verbindung mit TextAI-Tools zur besseren Identifizierung und Lösung von häufig auftretenden Problemen nach der Linienumstellung beitragen. Letztendlich trägt dies zu einem reibungsloseren und effizienteren Übergang zwischen verschiedenen Produkten oder Prozessen bei.
Erhöhung der Betriebszeit
Ungeplante Reinigungen
Reinigungsarbeiten sollten wie jede andere Wartungsaktivität behandelt werden. Ungeplante Stopps zur Reinigung der Linie erhöhen die nicht produktive Zeit und entfernen uns von unseren Produktionszielen. Aus diesem Grund können wir oberflächliche Reinigungen durchführen, die keine Unterbrechung der Produktion erfordern, wie tägliche Betriebsaufgaben, sowie tiefgehende Reinigungen während der geplanten Stillstände der Produktionslinie.
Wir können Reinigungen während der Linienumstellung oder wöchentliche Reinigungen planen. Dadurch wird die Wahrscheinlichkeit ungeplanter Stopps reduziert.
Verringerung der MTTR (Mean Time To Repair)
Durch die Verringerung der Mean Time To Repair können wir ungeplante Ausfallzeiten minimieren, was zu einer höheren effektiven Produktionszeit führt. Daher ist es wichtig, dass Reparaturverfahren auf klare und effektive Weise durchgeführt werden, unter Nutzung der Erfahrung früherer Reparaturen durch Mitarbeiter des Unternehmens an denselben oder ähnlichen Maschinen. Dies beschleunigt nicht nur den Reparaturprozess, sondern stellt auch sicher, dass wir die erforderlichen Ersatzteile haben, um die Reparatur schneller und effektiver durchzuführen.
CIP / SIP: Reinigung vor Ort / Sterilisation vor Ort
Der Reinigungs- und Sterilisationsprozess vor Ort (CIP/SIP) ist ein wichtiger, aber oft zeitaufwändiger Prozess. Es kann Stunden dauern, um einen vollständigen Sterilisationslauf durchzuführen. Isoliere alle ungeplanten CIP/SIP-Läufe und identifiziere die Gründe für diese zusätzlichen Läufe. Durch die Reduzierung dieser Sterilisationsläufe kannst du Stunden Maschinenstillstand und Arbeitszeit sparen.
Schulungslücken
Unter den Mitarbeitern ist es üblich, Schulungslücken und Wissenslücken zu haben, die effektiv behoben werden müssen, um sie zu minimieren und zu verhindern, dass sie ein Risiko für die Sicherheit und die operative Kontinuität der Produktionslinie darstellen. Dies könnte zu Fehlern bei der Schließung dieser Lücken führen.
Mit TextAI können Sie sehen, welche Art von Problemen sehr häufig auftreten. Durch eine Wurzelursachenanalyse können Sie die Probleme identifizieren, die möglicherweise nicht gut durchgeführt werden. Hier sind potenzielle Schulungslücken.
Wartungsanrufe für Probleme, die eigentlich von einem Operator behoben werden sollten, sind ebenfalls ein Hinweis auf eine Schulungslücke.
Finden Sie die Gründe für Wartungsanrufe heraus und identifizieren Sie die Gründe, die vom Operator abgedeckt sein sollten.
TextAI-Tools können uns auch dabei helfen, diese Lücken zu reduzieren, indem sie auf die in den Serviceaufträgen der Operator und Instandhalter dokumentierten Informationen zugreifen und sie für weniger geschultes Personal zugänglich machen, um sie bei der Ausführung ihrer Aufgaben zu unterstützen und ihnen zu helfen, die bereits aufgetretenen Probleme und deren Lösungen zu verstehen.
Reduzierung von "Wartungsanrufen"
Wartungsteams sind oft sehr beschäftigt, und das Warten auf das Eintreffen des Wartungspersonals bedeutet verlorene Zeit in der Produktion und zusätzliche Arbeitsbelastung für die Instandhalter. Wenn Sie alle Gründe für Wartungsanrufe analysieren, können Sie manchmal Aufgaben finden, die nicht allzu komplex sind und den Operatoren beigebracht werden können. Aufgaben, die häufig auftreten, wie beispielsweise Teilewechsel und Softwareparameter, eignen sich gut dafür, den Operatoren beigebracht zu werden.
Standard-Fehlerbehebungshandbücher können ebenfalls hilfreich sein. Beispielsweise könnte das Team beigebracht werden, vor dem Anrufen um Hilfe häufige Fehlerbehebungsschritte zu unternehmen, um viele Anrufe zu reduzieren.
Sicherheit und Mitarbeitergesundheit
Es ist auch wesentlich, die Möglichkeit potenzieller Ausfälle zu bewerten, die die Sicherheit der Mitarbeiter und der Umwelt gefährden. Zum Beispiel gibt es Vibrationen von einer Maschine, die andere Maschinen aus dem Takt bringt und vor allem bei den Mitarbeitern Unwohlsein verursacht. Aus diesem Grund ist es wichtig, eine Kritikalitätskarte unserer Ausrüstung und Prozesse zu haben und sicherzustellen, dass diese potenziellen Ausfälle in die Analyse einbezogen werden.